Presses électriques
Des solutions spécifiques pour répondre à vos besoins
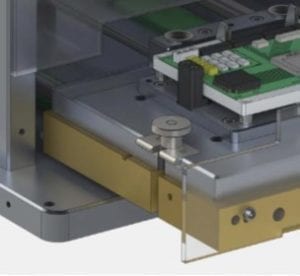
L’extrême souplesse de la presse de montage électrique KB TECH permet d’envisager une multitude d’applications, dans tous les secteurs d’activités. En plus d’être enregistrées, les données de pressage sont analysées pour la totalité des cycles afin de contrôler la qualité de l’assemblage.
La garantie d’une flexibilité totale
Les éléments mécaniques de transmission ont été choisis avec la plus grande attention afin de garantir un jeu de fonctionnement minimal entre la motorisation et l’outil afin d’offrir un positionnement précis.
Équipée de série d’un capteur de force implanté au plus proche de l’outil, la presse de montage électrique KB TECH permet une mesure de force en temps réel ainsi qu’une détection des collisions et frottements anormaux, en compression comme en traction.
L’afficheur tactile permet d’accéder aisément aux réglages de vitesse, de position et de force afin d’optimiser le déroulement du process. Ce mode est verrouillé par mot de passe afin de limiter son accès au personnel de maintenance.
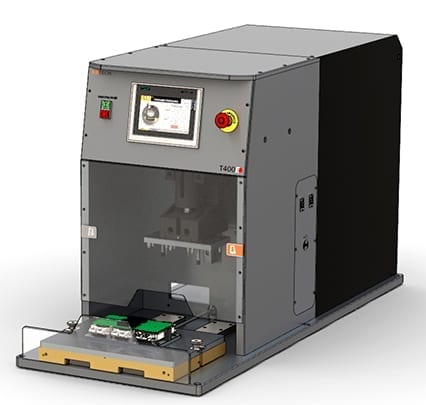
la qualité au coeur du process
Les chaînes d’acquisition sont dimensionnées de manière à permettre une caractérisation particulièrement fidèle du pressage, avec une valeur d’effort tous les centièmes de millimètre. Les données sont stockées dans l’équipement et représentées sur l’afficheur sous forme de graphiques de force (N) en fonction de la position (mm).
En plus d’être enregistrées, les données sont analysées pour la totalité des cycles afin de contrôler la qualité de l’assemblage. Pour cela, des critères de pressage sont mis en place afin d’encadrer la courbe d’effort (N) ainsi que la dérivée mathématique associée (N/mm). Afin de pouvoir faire abstraction des tolérances de hauteur propres aux composants à assembler, les conditions de fin de pressage et les critères d’analyse peuvent être définis relativement à un seuil de déclenchement paramétrable (trigger). Celui-ci correspondant à un début de montée en effort.
Une traçabilité à 100%
De part sa conception reposant sur l’utilisation d’un API modulaire et extensible, la presse de montage électrique KB TECH se montre particulièrement évolutive. Disposant de série de 2 ports Ethernet libres et d’un port USB en façade, elle peut par exemple aussi accueillir une interface sérielle, une ligne Profibus ou des entrées/sorties supplémentaires. Elle se montre ainsi parfaitement adaptée pour être intégrée à tout type de système de traçabilité.
Port USB : situé en façade de la presse, celui-ci permet une récupération de l’ensemble des données de pressage à l’aide d’une clé USB. Celles-ci sont exportées sous forme de fichiers CSV.
Ports ethernet (2x) : ils permettent par exemple le branchement d’une console de programmation et l’interfaçage avec le réseau usine. Une télémaintenance de l’équipement est également rendue possible.
Lecture code-barres : afin de permettre une identification fiable d’un produit ou d’un lot de composants, un lecteur de code à barres portatif ou fixe peut être connecté à la presse.
Contrôle par visions : si un contrôle de l’assemblage pressé est nécessaire, un capteur ou un système de vision peuvent être intégrés directement dans la cage de la presse.
Une convivialité optimale au service de la productivité
La conception singulière de la presse de montage électrique KB TECH place véritablement l’humain au centre du process. L’accessibilité, la convivialité et la sécurité ont fait l’objet d’une attention toute particulière et rendent l’équipement aussi agréable à utiliser que performant.
La mise en place des composants se fait sur un tiroir en dehors de la zone de pressage de manière à améliorer les conditions de chargement et à offrir à l’opérateur une sécurité d’utilisation optimale. Le tiroir est mis en mouvement à l’aide d’un actionneur pneumatique alimenté en basse pression afin de simultanément garantir un transfert rapide et éviter tout risque de coincement.
Le départ du cycle est déclenché par un bref passage de la main devant une touche sensitive placée en façade de la presse, à proximité de la zone de chargement. Elle ne nécessite pas un appui prononcé et un simple effleurement est suffisant.
Durant le pressage l’opérateur a les mains libres et peut ainsi effectuer des opérations en temps masqué.
Situé en façade de l’équipement, il donne à l’opérateur les informations essentielles au bon déroulement des cycles de pressage : état de l’équipement, numéro de production, cycle OK ou NOK, prévisualisation de la courbe force/position, etc. Des écrans dédiés au paramétrage et au diagnostic permettent au personnel de maintenance de configurer le profil de pressage et de bénéficier d’une aide à la résolution d’erreurs et de pannes. L’afficheur est basé sur Microsoft Windows CE et permet par exemple à l’utilisateur de connecter des périphériques USB (clavier, clé USB) ou d’utiliser l’explorateur du système d’exploitation.
Simplicité et efficacité
Le tiroir ainsi que le porte-outil supérieur sont dotés d’interfaces mécaniques permettant un changement d’outils aisé, sans clé. Si les applications le nécessitent, le tiroir peut embarquer des répartiteurs électrique et pneumatique permettant à l’outil inférieur d’être équipé d’actionneurs et/ou de détecteurs. Il est ainsi par exemple possible de vérifier la présence de composants avant de lancer un cycle ou de maintenir ces derniers à l’aide de vérins.
Un détrompage mécanique empêche une mise en place incorrecte de l’outil tandis qu’une vérification logicielle est réalisée pour contrôler la correspondance entre les outils supérieur et inférieur (poka-yoke). Cette identification permet également à la presse de montage électrique de sélectionner automatiquement le programme de pressage adéquat, sans nécessiter la moindre intervention sur l’afficheur.
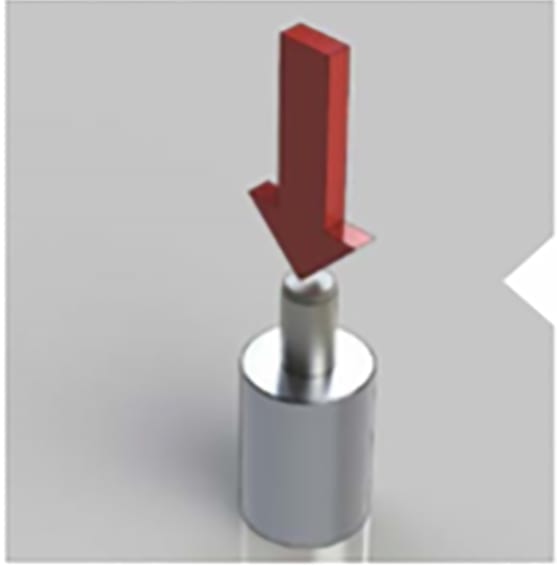
Arrêt en position
L’outil descend jusqu’à atteindre une position définie. Il peut s’agir d’une position absolue ou relative afin de pouvoir faire abstraction des tolérances de hauteurs sur les composants. Si les efforts mis en jeu sont importants, une compensation des déformations de la presse peut être mise en place afin d’affiner la précision du positionnement.
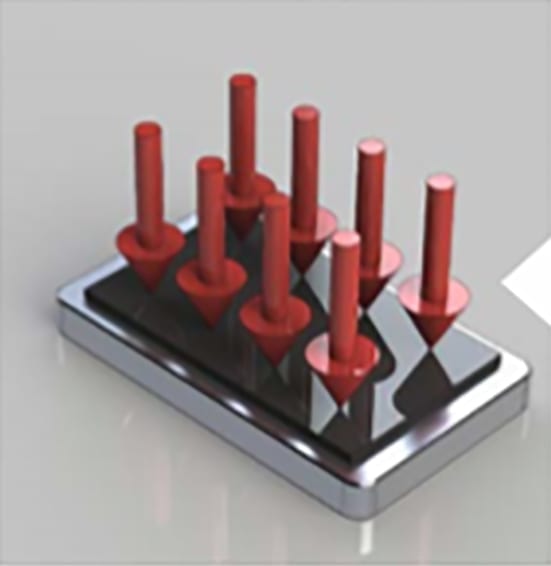
Arrêt en effort
La presse se déplace jusqu’à atteindre un effort programmé. Celui-ci peut être maintenu pendant une durée donnée si nécessaire. Ce profil de déplacement permet également un arrêt précis et rapide sur butée afin de garantir que les composants à assembler soient parfaitement plaqués l’un contre l’autre.
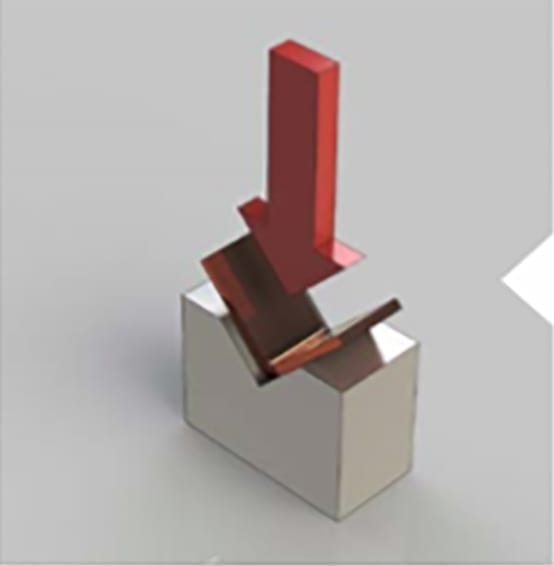
Arrêt en raideur
La descente de la presse est stoppée lorsqu’un rapport force/effort correspondant à une raideur de l’assemblage est obtenu. Une condition d’arrêt de ce type peut être nécessaire pour assurer l’étanchéité de certains types de bouchons pneumatiques ou hydrauliques.