Presses pneumatiques
Des solutions spécifiques pour répondre à vos besoins
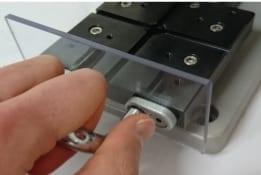
La presse de montage pneumatique KB TECH constitue une parfaite alternative aux presses manuelles classiques dès lors que la cadence, l’effort nécessaire ou les exigences en terme de qualité sont des critères importants. KB TECH vous propose une gamme d’équipements qui couvre de vastes plages d’efforts, de courses de travail et de dimensions.
Une large gamme, de 0,75 à 140 kN
Les presses de montage KB TECH sont équipées de vérins pneumatiques à poussée directe, dotés d’une ou plusieurs chambres, générant un effort constant sur toute la course. Pour les applications nécessitant une force plus importante, un vérin pneumo-hydraulique peut être utilisé. Celui-ci se caractérise par une poussée maximale sur les derniers millimètres de course, sans utilisation de centrale hydraulique.
Équipée de série d’un API et d’un contrôle de la position fermée du tiroir par un relais de sécurité, la presse de montage KB TECH constitue un équipement «clé en main» pouvant être utilisé en toute sécurité sans intégration spécifique.
La mise en place des composants se fait sur un tiroir en dehors de la zone de pressage de manière à améliorer les conditions de chargement et offrir à l’opérateur une sécurité d’utilisation optimale. Dans le cas d’une presse à tiroir (série P), le départ du cycle est déclenché par un bref passage de la main devant une touche sensitive placée en façade de la presse, à proximité de la zone de chargement. Elle ne nécessite pas un appui prononcé, un simple effleurement suffit. Durant le pressage l’opérateur a les mains libres et peut ainsi effectuer des opérations en temps masqué.
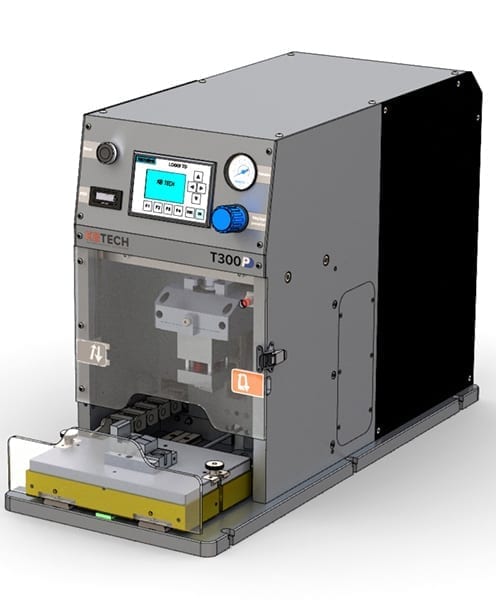
UNE modularité à 100%
Le manodétendeur et le manomètre situés en façade de l’équipement permettent d’agir sur la pression du circuit pneumatique. Celle-ci est proportionnelle à l’effort généré par le vérin.
Un afficheur peut être intégré afin de fournir à l’opérateur les informations essentielles au bon déroulement des cycles. Des écrans dédiés au paramétrage et au diagnostic peuvent également être proposés.
Afin de permettre une identification fiable des produits, un lecteur de code à barres peut être connecté à la presse. Les données de pressage peuvent être enregistrées dans une base de données ou envoyées sur le réseau usine.
Nous intégrons sur demande de nombreuses autres fonctionnalités : mesures de la force et du déplacement, capot mobile, posages ESD, détection de la présence des composants, etc.
Simplicité et efficacité
Le tiroir ainsi que le porte-outil supérieur sont dotés d’interfaces mécaniques permettant un changement d’outils aisé. Si les applications le nécessitent, le tiroir peut embarquer des répartiteurs électrique et pneumatique permettant à l’outil d’être équipé d’actionneurs et/ou de détecteurs. Il est ainsi par exemple possible de vérifier la présence de composants avant de lancer un cycle ou de maintenir ces derniers à l’aide de vérins.
Un détrompage mécanique empêche une mise en place incorrecte de l’outil tandis qu’une vérification logicielle est réalisée pour contrôler la correspondance entre les outils supérieur et inférieur (poka-yoke). Cette identification permet également à la presse de montage pneumatique de sélectionner automatiquement le programme de pressage adéquat, sans nécessiter la moindre intervention de la part de l’opérateur.
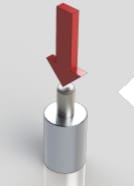
Emmanchement – clipsage
La position finale des pièces peut être réglée par la butée basse à pas fin ou la mise en butée de positionnement par le produit.
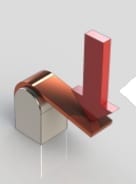
Pliage
Le profil des plis est déterminé par la géométrie de l’ensemble poinçonmatrice et peut être ajusté grâce au réglage de la butée basse et/ou l’action de poinçons latéraux fixés dans la cage de la presse.
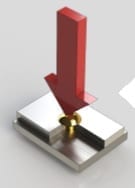
Rivetage
Une butée réglable à pas fin associée à une temporisation en position basse permettent de compenser l’élasticité des matériaux et obtenir un rivetage précis.